> Products > Sandwich Panel Production Line > EPS sandwich panel machine (Continuous)
EPS sandwich panel machine (Continuous)
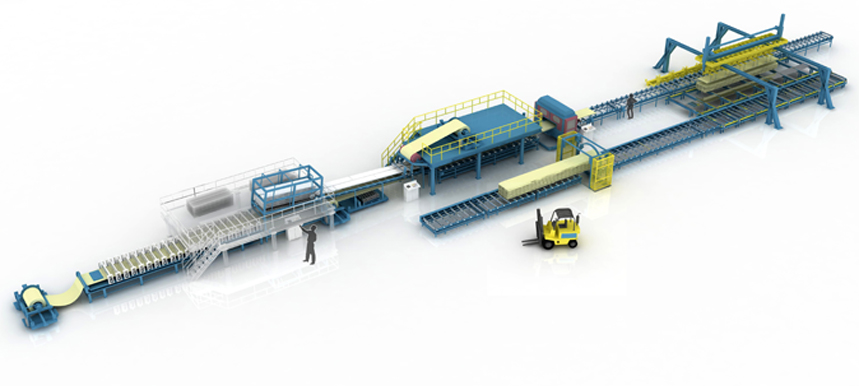
Expanded polystyrene is white and lightweight material with excellent water-proofing, thermal insulation, soundproofing and buffering properties, and our Expanded Polystyrene Sandwich Panel Producing Equipment, using it as insulator, is the automation equipment that can continuously and efficiently produce expanded polystyrene sandwich panels of exquisite and diverse shapes.
This equipment has the advantages such as high durability, easy management, technology equivalent to those of advanced European companies and relatively competitive price, and is the excellent facility with the largest market share in Korea. Besides, it has been exported to Asia, Middle East, and Central & South America and so on, and is well received from customers.
Our EPS continuous production line is designed to produce the panels for use in roofing and walls, such as cold storage, general storage, factory buildings, temporary buildings, prefabricated buildings that can produce the most cost-effective way.
Designed in the production rate of 5 ~ 12m / min production facilities, production facilities and flexible can be easily expanded by the addition of a molding machine to produce panels of various types as needed
Expanded Polystyrene Sandwich Panel Producing Line consists of Un-coiler that inputs and releases coil, Roll Forming Unit that makes shape of coil, E.P.S. Board Supplying System that inputs expanded polystyrene board and properly cutting/processing it, Side & Surface Trimming System that cuts the binding sites and surface of panel in accordance with the required specification, Glue Applying System that applies bond to attach steel plate and expanded polystyrene, Laminating Unit that makes the shape of sandwich panel, Panel Cutting Unit that cuts the fabricated sandwich panel, Auto Stacking Unit that loads the finished panels, and Panel Packing Unit that packs the loaded panels with plastic wrap and discharge them.
Un-Coilers & Entry parts
Un-coiler is a device that inputs steel coil to the upper and lower parts of sandwich panel to feed it stably. The mandrel type operated automatically by a hydraulic and it’s convenient to control and sophisticated. 2+2 system production equipment unit doesn’t need to stop to load the new coil set, which it helps to continue to produce high capacity of panels.
Roll forming unit
It is a device that continuously gives shape to sandwich panel as steel coil fed from Un-coiler is engaged between the upper and lower sections of a metal roller.
Usually it makes the beautiful and delicate shape of variety wall and roof type panel. It designed in cassette type and rail way wheel type to easily change to make different shapes.
Expanded polystyrene supplying system#1 : General joint type
It is an ordinary Expanded Polystyrene Board Supplying System, which supplies 2 expanded polystyrene boards to the equipment in zigzags.
Expanded polystyrene supplying system #2: Finger joint type
It was designed for manufacturing thick and rigid sandwich panels used at cold storage and so forth, and the system continuously supplies boards in front and in the rear using the grooves of finger joint.
Side & surface trimming system
This device trims the combining part and surface of panels in accordance with the required specification. According to the shape of the panel will be cutting sophisticated and elegant.
Glue applying system
It is a device applying glue, and this facility adopts the mixing system that is inexpensive, durable and widely used all over the world.
There are mixing type and spray type to apply the glue. The mixing type method is widely used throughout the world as the price is relatively inexpensive and durable. However the spray type method is a little expensive but can save a discharge the rate of the glue and application amount.
Laminating unit
It is a device that makes the shape of sandwich panel applying constant pressure and heat to the upper and lower steel plates where glue is applied.
Acquired patent applications (Patent No. 0,304,450) a rubber roller system laminating unit has low power consumption and inexpensive compared to the double belt conveyor system and the flatness of the product remains good.
Panel cutting unit
A device that cuts sandwich panel fabricated at Laminating Unit to the length desired by users using a band saw. Different types cutting such as wheel cutting and band saw cutting has developed to correspond for the customer’s needs.
Auto stacking unit
As is a device that automatically stacks the finished panels, the quantity desired by users can be loaded continuously by loading pattern of vacuum suction plates or lift conveyor And in case of roofing material, cross stacking is available, if necessary.
Panel packing unit
A device that packs panels loaded at Auto Stacking Unit with plastic wrap on 4 sides or 6 sides and discharges them. Applying pallet systems to insert the EPS block automatically and it makes handy for cargo transportation and storage the panels.
<Specification : sandwich panel line>
1. | Producing Speed | : | Max. 7~10 m/min |
: | Max. 7~10 m/min | ||
: | The speed can be changed as below conditions. | ||
: | a. the type of glue | ||
: | b. temperature of mixing area | ||
: | c. thickness panel, length. | ||
Width | : | 1000mm | |
Thickness | : | 50 ~ 200mm |
<The general specification of PU panel produced>
2. | Electric power source | ||
Commercial voltage | : | According to customer’s specification | |
Total power | : | 130Kw | |
3. | Raw Material | : | Pre-painted galvanized steel sheet. ASTM A 526-85 / JIS G 3302 SGCC or other same class of soft material. |
Coil Thickness | : | 0.4 ~ 0.7mm | |
E.P.S Size | : | For main board (It is just our standard, changeable by buyer) | |
: | (L) 3600 meter * (W) 500m* (T) 50 ~ 200mm For roof pad | ||
: | (L) 1500 meter * (W) 600m* (T) mm ( same as roof height) |
Profiles: Expanded Polystyrene(EPS) sandwich panel production line (Continuous)

IKEP-RF-4R
- Coil width : 1219/1040mm
- Product width : 1000mm
- Thickness : 40~200mm
- Coil thickness : 0.4~0.7mm
- Depth of Roof : 35mm

IKEP-WA-G
- Coil width : 1040/1040mm
- Product width : 1000mm
- Thickness : 40~200mm
- Coil thickness : 0.4~0.7mm

IKEP-SF-1R
- Coil width : 1105/1040mm
- Product width : 1000mm
- Thickness : 40~200mm
- Coil thickness : 0.4~0.7mm

IKEP-SF-3R
- Coil width : 1219/1040mm
- Product width : 1000mm
- Panel thickness : 40~200mm
- Coil thickness : 0.4~0.7mm

IKEP-SF-SD
- Coil width : 1219/1070mm
- Product width : 1000mm
- Thickness : 50~200mm
- Coil thickness : 0.4~0.7mm

IKEP-ZSF-M
- Coil width : 1200/1070mm
- Product width : 1000mm
- Thickness : 50~200mm
- Coil thickness : 0.4~0.7mm

IKEP-ZRF-5R
- Coil width : 1250/1070mm
- Product width : 1000mm
- Panel thickness : 50~200mm
- Coil thickness : 0.4~0.7mm
- Depth of roof : 34mm

IKEP-2WA-M
- Coil width : 1070/1070mm
- Product width : 1000mm
- Panel thickness : 50~200mm
- Coil thickness : 0.4~0.7mm
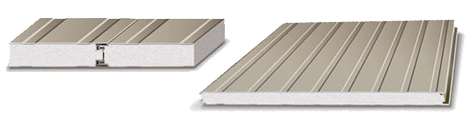
IKEP-ZWA-P
- Coil width : 1070/1070mm
- Product width : 1000mm
- Panel thickness : 50~200mm
- Coil thickness : 0.4~0.7mm
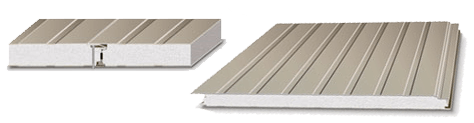
IKEP-ZSF-P
- Coil width : 1200/1070mm
- Product width : 1000mm
- Panel thickness : 50~200mm
- Coil thickness : 0.4~0.7mm

IKEP-C30
- Coil width : 1219/1040mm
- Product width : 1040mm
- Panel thickness : 50~200mm
- Coil thickness : 0.4~0.7mm
- Depth of roof : 34mm
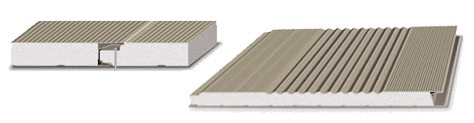
IKEP-C45
- Coil width : 1100/1040mm
- Product width : 1000mm
- Panel thickness : 50~200mm
- Coil thickness : 0.4~0.7mm
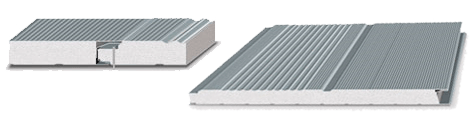
IKEP-C30F
- Coil width : 1180/1040mm
- Product width : 1040mm
- Panel thickness : 50~200mm
- Coil thickness : 0.4~0.7mm
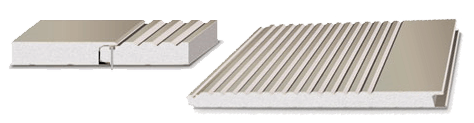
IKEP-V50
- Coil width : 1219/1040mm
- Product width : 1040mm
- Panel thickness : 50~200mm
- Coil thickness : 0.4~0.7mm